Past November 2019 we had the opportunity to teach a class of Digital Fashion Making at Arca textile lab (Palermo), thanks to the collaboration with WeMake and Fastweb Digital Academy.
Here a part of the interview made by WeMake to one of our students :
Luca Lavore
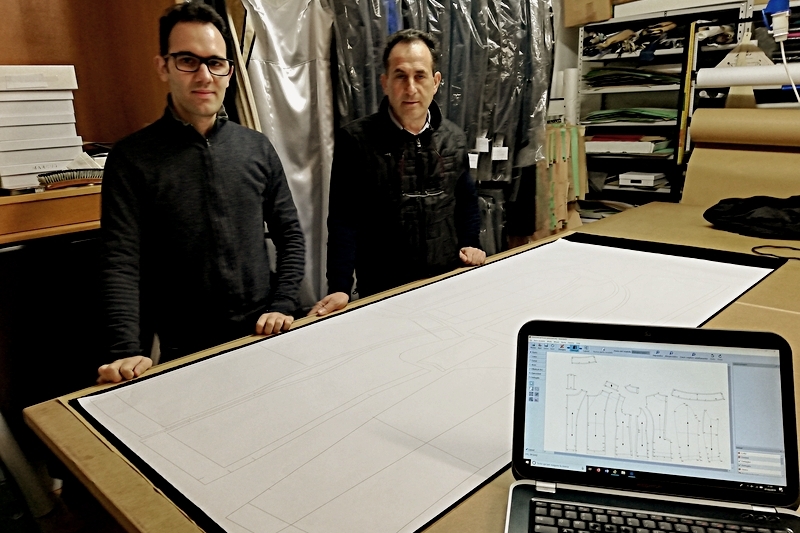
Why did you decide to attend Digital Fashion Making course?
I received an indication and searched online what kind of software we were going to use during class. Helping my family in our Atelier management and being interested in technology within the clothing sector, I found it tempting to learn how to use Seamly2D open source software: from the very first time using it, Seamly2D seemed immediately very intuitive.
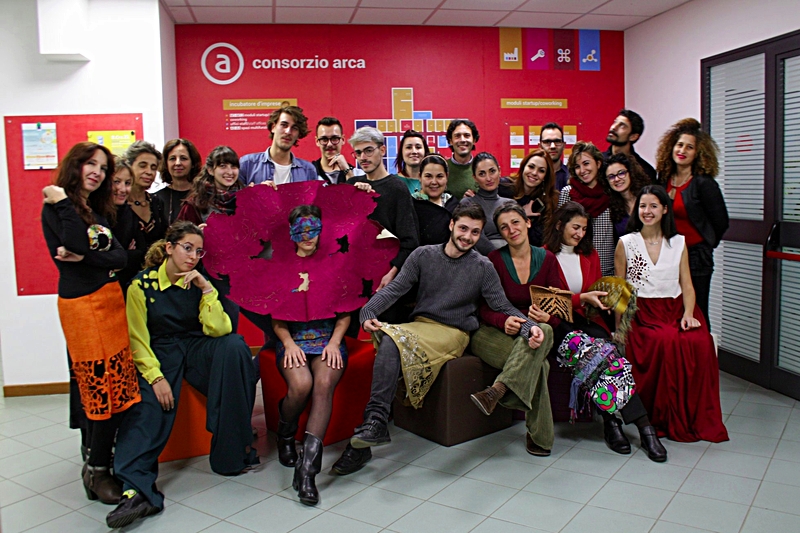
Was it useful for your work?
After an intensive week between CAD models and the use of lasercutter, I had very clear ideas on how to implement the software in the family business production process for at least three main reasons:
1. the nature of parametric software with dependent elements of Valentina / Seamly2D, which perfectly matches the needs of a modern tailor who has adopted proportional modeling systems based on the study of the human body;
2. the gratuitousness, at the antipodes to the prohibitive figures of the most renowned software, often designed exclusively for industrial use;
3. the perfect correspondence between the cutting method on paper placed and the ratio of the software that includes a printout as project output. The old (and enemy of precision) approach of signing directly on the fabric with chalk would not find valuable help in the use of software as it lacks the fundamental shift to modern placement systems.
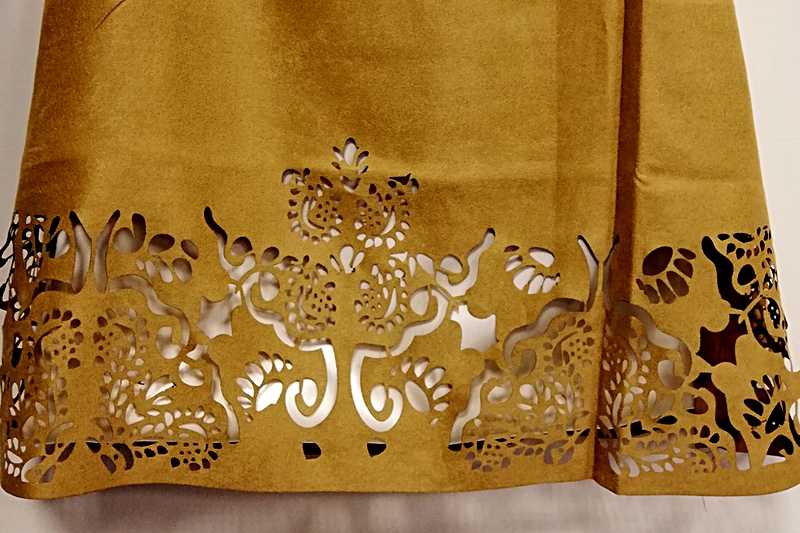
How did you apply the knowledge acquired at work?
The purchase of a plotter, a valid and indispensable tool to accompany the software, allowed me to speed up the entire packaging process of a garment by about 25% . Vector drawing printing has appreciably increased the accuracy of the models compared to the previous method of manual tracing. The other advantages found, common to anyone who makes use of CAD programs, are surely the best forecasting capacity on the result of the garments, smaller footprint of cartons and greater general flexibility in responding to customer requests.
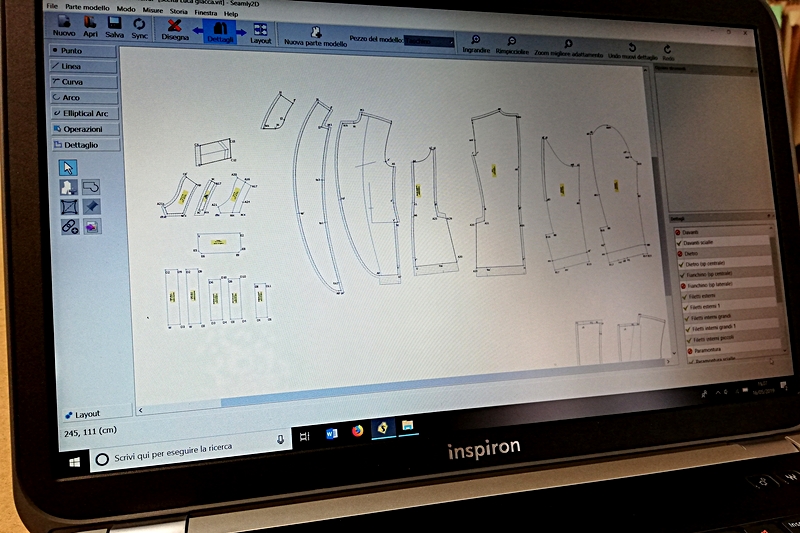
What would you say to a person who has the possibility to follow a course focused on the use of Seamly2D software?
The advice I can give to anyone who has the possibility to follow a course related to this software is to leave any prejudice, whether deriving from a possible background more oriented towards fashion design than patternmaking, whether it is about working in a more traditional way – rejecting any new instrument / approach. Patternmaking is a science that transcends all the educational fields of the clothing field, knowing its principles and integrating them with the use of IT tools without having to pay the high costs that often entails is an opportunity not to be missed.
To read the blogpost complete follow the link to the wemake page!